360m2烧结机是某公司生产的龙头设备。360m2烧结成品振动筛筛分系统是对进入高炉的所有矿石物料进行精细筛选。矿石物料通过360m2烧结成品振动筛筛分系统筛选后称之为精料,精料提供给高炉进行冶炼。精料对提高高炉系数与高炉的顺利生产起着决定性作用。成品振动筛筛分系统主要有振动筛与传送系统等部分组成,振动筛是高炉生产运行中的关键设备之一,它的工作效率直接决定高炉的生产效率。
2、 360m2烧结成品振动筛系统工作原理
360m2烧结成品振动筛系统中主要设备是振动筛,振动筛主要由激振源和筛体等部位组成,筛体主要有筛箱和筛网等部件,在工作中激振源带动筛体进行高频振动,物料经过高频振动的筛体被筛分。
如图1所示,天津钢铁集团有限公司360m2烧结成品振动筛使用的是直线筛,筛网采用梳齿筛网,梳齿筛网为锻压件,其安装形式为搭接连接,筛网与水平方向的夹角约为7°~16°振动筛所用功率为2x45kW=90kW。
3 、360m2烧结成品振动筛存在的问题
通过实际使用,发现高炉矿槽振动筛存在如下问题:
1)筛分效率低,仅为75qo左右,物料筛分不彻底,成品料中含粉量过高,使高炉透气性差,影响了高炉的正常运行。
2)在筛网使用寿命的后期,筛孔逐渐变大,筛下物的颗粒度严重超标。
3)振动筛振幅为11mm,对物料破碎性很大。
4)振动筛筛网使用寿命短,从实际使用结果看,梳齿筛网使用寿命大约在四个月左右。
5)激振器的轴承容易发热,轴承的使用寿命短,事故率较高。
4、产生的原因分析
1)因振动筛采用梳齿筛网,其开孔率为15%~25%,导致临界颗粒卡孔特别严重,物料卡孔后不易排出。
2)筛网网孔不变化,使用寿命的后期,筛孔逐渐变大,造成筛下物的颗粒度易超标、使用寿命短。
3)振动筛的自重较重,且振幅较大,为7mm~12mm。使选择的激振器较大,结果使轴承容易发热,造成轴承的寿命降低,事故率较高。
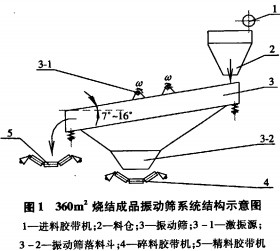
5、解决方案
1)改变筛网结构设计,解决在运行过程中筛分效率低、筛孔卡孔的问题
针对所用梳齿筛网的缺点,通过对比,将筛网改为棒条结构,筛网材质为高锰钢,筛网孔形状设计成上部为直筒、下部为倒锥形的棒条筛孔。此种网孔形状设计其开孔率可达300/0一40%。并且运行过程中筛孔是在高频变化的,从而临界颗粒不易卡孔。
2)改变筛网安装倾角,减少振动筛的自重,降低设备事故发生率
原振动筛为了增加物料在筛网上跳动的次数,增加一些透孔的概率,其筛网倾角比较小,大约7°到16°,为了减少振动筛的自重,降低设备事故发生率,将振动筛筛网与水平方向的倾角加大,改为:27°~29°,如图2所示,因筛网与水平方向的倾角加大,在相同高度的前提下,可使振动筛的水平长度减少,从而减少振动筛的自重。
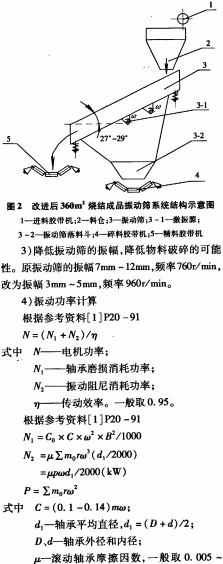
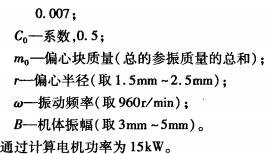
6、振动筛改造后的使用效果
1) 360m2烧结成品振动筛改造后,经过4年多的使用,每天筛分烧结矿筛网筛下返矿率比改造前下降了3%~4%。每天返矿大约在400t左右,每年累计少返矿7万t左右。改造后一年可以节约几百万的成品费用。
2)改造后,筛网使用过程中筛分效果不会发生明显变化。筛分效率高可达90%以上,大大降低了成品料中的含粉量,从而提高了高炉系数。
3)改造后使用了棒条筛网结构,筛网不会随着时间的延长而迅速发生变化(注:开孔率=开孔面积/总的筛网面积),筛网使用寿命可达12个月。
4)延长了更换周期,节省了更换筛网的工时和降低了其工作强度。
改造前,更换筛网需要6个人,工作12h,而改造后,因使用棒条筛网,更换其只需要三个人、工作2.5h就可以完成。
5)改造后整机重量比以前大幅减少,其重量约是以前的60%;随着重量大幅减少,耗电也相应减少了约60%。
6)改造后激振器比改造前大大减小,使轴承不容易发热,轴承的寿命大大提高,加油系统不容易漏油,设备现场得到了改善,故障发生率大幅降低。
7、结束语
360rri2烧结成品振动筛改造后:
1)提高了筛分效率,减少了安装空间。
2)筛子的进出口用软接头密封连接,使整个筛分作业在全密封状态下进行。
3)节能环保方面得到了改善。
4)高炉的系数得到了很大提高。
5)每年可以节省电费:约6. 57万元(工业用电按1元/kW.h计算)