目前饲料厂家在生产膨化料时常见的工艺布置如图1。
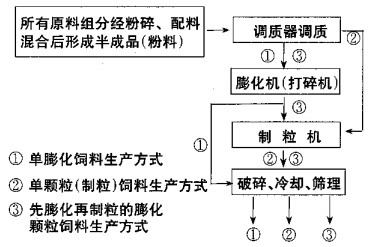
只购买一台膨化机安装在原有制粒系统的调质器之后,在颗粒机之前,并且在调质器到膨化机之间、膨化机到制粒机之间装二道气动三通,膨化机出口有一台打碎机。这种工艺布置有较大的灵活性,膨化机和制粒机共享一台调质器,既可以通过“调质一膨化”生产单纯的膨化料(不规则的块片状),又可以通过“调质一膨化一颗粒机制粒”生产膨化颗粒饲料,并且仍然可以通过“调质一制粒”不经膨化生产普通的颗粒饲料。
这种工艺布置虽然给生产企业带来较大的方便,但经过许多科研机构、专家学者的研究、分析以及饲养者的饲喂试验都说明,这种先膨化再制粒生产膨化颗粒饲料的方法,有很大的负面效应:1)维生素的损失。膨化制粒的温度、压力、摩擦和水分都会导致维生素的损失。2)酶制剂的损失。因为酶是一种蛋白质,一般酶的适宜温度为35~40℃,最高不超过50℃,而膨化制粒过程中通常温度都在100℃以上,并伴有高压、高湿,因此大多数酶制剂的活性将损失殆尽。3)微生物制剂的损失。目前饲料中应用较多的微生物制剂主要有乳酸杆菌、链球菌、酵母、芽孢杆菌等,这些微生物制剂对温度尤为敏感,当膨化制粒温度超过85℃时其活性将全部丧失。
鉴于目前传统工艺的负面效应,已经有许多科研院校、企业单位参与研究避免或减少上述热敏性物质损失的膨化工艺研究。这里介绍一种生产膨化颗粒饲料新工艺,其工艺流程见图2。

利用目前现有设备条件应用新工艺可最大限度地降低维生素、酶制剂等热敏性物质的损失,降低到普通非膨化普通颗粒饲料对热敏性物质的影响水平,甚至低于普通颗粒饲料影响程度。
新工艺的原理是把原料组分区分开,在生产过程中分阶段加入:无需膨化部分及对热敏感的添加剂、维生素类不经过膨化过程,而只膨化大宗原料(原粮)部分,达到淀粉糊化、抑制抗营养因子活性、杀菌等目的。膨化后的大宗原料经粉碎后与未经膨化的原料组分配合,再一起制粒出成品膨化颗粒饲料。由于热敏性物质只经过普通的一次制粒,而未经过膨化的高温、高压、高湿条件加工过程,因此维生素、热敏性添加剂等损失比传统膨化后再制粒工艺要小得多,而与普通制粒工艺无差异。
新工艺无需改变原有传统工艺的调质、膨化、制粒的工艺布置,但需要在膨化后到粉碎之间增加水平输送设备、设施,条件许可也可采用自流管。调质、膨化、制粒之间物料流向仍是利用原有的三通开关来控制。新的工艺运用不影响传统工艺中生产单膨化饲料及普通颗粒饲料的方式。但由于大宗原料膨化后需经过二次粉碎和二次配料,必然会对生产的效率和加工费用等带来一定的影响。