秦皇岛发电有限责任公司(下称秦电)大型离心风机曾多次发生主轴磨损故障,致使风机振动加剧,无法维持稳定运行,被迫停运检修,处理困难且所需时间较长,严重威胁机组的稳定运行。1999年至今先后10台次处理轴颈,其中6次在机组运行时被迫停运风机检修处理,直接影响机组的稳定运行。本文主要针对此类故障进行深入分析并介绍了采取的有效防范措施。
1、故障案例
案例-:2005年5月,2号炉2号一次风机振动增大到o.2 mm,停运解体,发现承力侧轴承内圈转套,紧定套锁紧螺母松动,虽因抢修没有拆下轴承进行轴颈测量,但判断轴颈已有磨损。
案例二:2002年,1号炉号1号一次风机推力侧轴颈磨损0-10~0. 15 mm,先后3次因振动超标无法维持运行而退出运行检修,于当年9月小修进行补焊加工修复。
案例三:2004年7月,3号炉B-次风机推力侧轴颈磨损0. 05~0.15 mm,先后3次因振动超标无法维持运行而退出运行检修,于2005年1月份小修时进行补焊加工修复。
案例四:2005年1月3号炉小修时检查发现A一次风机推力侧轴颈磨损0. 07~0.13 mm,进行刷镀修复处理。
案例五:2004年10月2号炉小修时检查发现1号引风机推力侧轴颈磨损,磨损量为0. 20~0. 29 mm,进行刷镀修复处理。
从以上案例可以看出,离心风机主轴磨损已严重影响秦电机组安全运行。
2、故障分析
主轴磨损的主要原因是轴承内圈与主轴轴颈的配合紧力不够,内圈与主轴的配合紧力小于运行时滚动体与内外套的摩擦力,导致轴承内套与主轴配合处产生相对运动。造成此类磨损的因素很多,主要有装配工艺中的配合偏差、轴承装配的工艺方法、联轴器两端面间隙偏差及对中偏差、运行方式等。
2.1装配工艺中的配合偏差
在轴承的配合上,重要的是给予承受负荷旋转的套圈合适的过盈量。配合面之间的过盈量在装配后和工作中是变化的,由于内圈滚道受载弧面上的切向变形和热张变形使得内圈变大,因而导致内圈和轴之间的过盈量减小,内圈与轴的配合变松,而外圈的张大则使外圈与外壳孔之间的过盈量加大。因此,在选择配合时一般应将内圈与轴的配合选得较紧一些,外圈与孔的配合选得较松一些。以运转中轴承温升说明,如轴承内部温度和外壳周围温度的温差为A℃,运行中内圈与轴温差引起配合量的减少导致跑套,一般此温差引起配合过盈量减少值由下面公式计算:
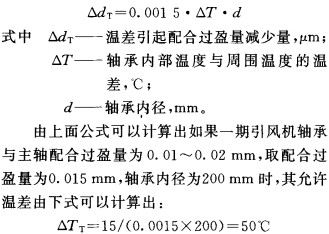
由此可以看出,轴承内圈温度超过环境温度50℃时轴承内圈的配合紧力即会消失而引发转套。
同时,配合面加工的凸凹点,由于装配作业时压损,有效过盈量比目标过盈量减小,一般因加工精度而异。30~150 mm左右的轴承的有效过盈量约为目标过盈量的95%。如果存在配合偏差,以上因素均可导致无法满足装配要求,引发主轴磨损及转套现象。
主轴与轴承配合有其设计标准,配合紧力过大会导致轴承游隙减小且套圈变形,运行时轴承发热,噪音增大,外圈转动。配合紧力过小会因紧力不足造成内圈转动。以一期一次风机的轴承装配为例,一期一次风机轴承定位是靠紧定套结构将轴承固定在轴上,如图1所示。
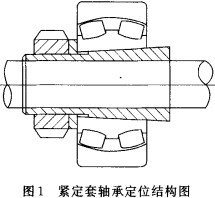
轴承结构为锥孔双列调心滚子轴承,用紧定套安装在圆柱轴上,靠锁母敲紧将紧定套与轴承定位在轴上。根据轴承手册,其配合紧力的大小是靠轴承紧固后的游隙变动量来确定。根据轴承公称内径范围,轴承的轴向方向压入量应为0.75~0.9 mm,径向游隙的减少量应为0.05~0.06mm,按照轴承的标准游隙0.17~0.22 mm计算,轴承装配后的轴承游隙值应为0.11~0.17 mm。且此测量值应在主轴顶起状态下,即避免因转子自重外圈变形导致测量偏差。但在实际装配中,往往对装配标准不清楚或对测量细节不认真,导致配合紧力不够,加之轴承运行中的内外温差因素,引发运行中轴承转套、主轴磨损故障。
轴承的定位精度是杜绝配合偏差的可靠保证。因此,在装配前,要准确测量各部配合尺寸,满足尺寸精度、形位公差及表面粗糙度配合要求。装配中对主轴的圆度、圆柱度和轴肩跳动均有公差标准,与O级精度轴承相配的轴的圆度公差为IT4/2,圆柱度公差为IT4/2,挡肩跳动公差为IT3,配合表面光洁度应达到6.3 S,尺寸公差应比形位公差低一个精度等级即IT4。其中配合处所有测量工作应以环境温度为20℃情况下测量为宜。考虑现场环境的不定性,配合尺寸应在现场相同环境温度下测量,确保配合尺寸数据的准确性。如果上述的装配尺寸保证不了,必然影响到装配紧力,比如安装部分的挡肩如果精度不好,就会导致轴承内外圈倾斜。3号炉B-次风机推力侧轴颈磨损后,在主轴圆周方向焊接焊道并手工修磨至配合尺寸,运行后又发生内圈转套、焊道磨损现象,主要原因即配合精度与要求的标准精度相差较大。
2.2轴承装配的工艺方法
大型风机轴承装配一般采用热装法,现场装配时用油或轴承加热器将轴承加热至100℃左右,将轴承套装至轴上,安装后马上用锁母紧固,并用塞尺测量轴承与轴肩是否有间隙。存在间隙说明轴承未装配到位,不能投入正常使用,因轴承加热后不仅在径向膨张。在轴向方向也有膨张。以3640轴承为例,其轴向宽度为138 mm,与加热温差100℃比较,其轴向膨张量由公式(△L—La△t)可以算出为0.165 mm。因此必须在轴承冷却后进行再紧固,以确保轴承的轴向紧力。引风机因通流介质温度较高,轴涨位移较大,如果轴向紧固力不足,易引发风机运行时轴承转套。
2.3联轴器两端面间隙偏差及对中偏差
联轴器的精确找正,可以保证转子的运转平稳、不振动。否则,将使轴和联轴器产生很大的应力,严重地影响轴、轴承的正常运转,因此联轴器的精确校正是检修装配中的一个重要环节。
秦电在装运行的大型离心风机联轴器型式有以下3种:一期送风机弹性圈柱销联轴器,一期引风机为尼龙柱销式联轴器,一、二期一次风机为刚挠性联轴器。
由图2显示,送风机弹性圈柱销联轴器,只要保证销孔与弹性圈之间留有一定的间隙(O,5~2mm),使两联轴器之间能沿圆周方向活动,该联轴器能够很好地消除机、电联接的轴向力。由图3显示,一次风机联轴器因轴向、径向偏差产生的轴向力通过簧片直接传递到轴承部。
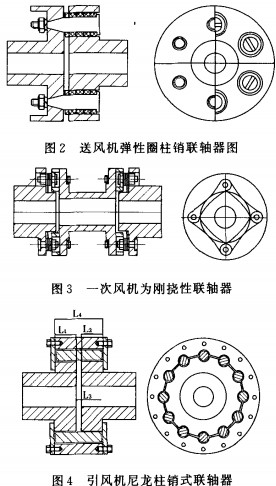
由图4可以看出,当引风机两对轮间隙超过给定值时,便产生了轴向力。其轴向力在运行中始终存在,电机轴瓦轴向允许移动量大,不受联轴器影响,风机承力侧轴承为自由轴承,可以自由伸缩,受轴向力影响较小。而风机推力侧轴承为风机的定位轴承,推力间隙一般为0.20~0. 40 mm,允许位移的变动量很小,如果联轴器间隙不当,由联轴器产生的轴向力在运行当中一直存在,推力轴承一直受交变轴向力作用,极易引发轴承转套。由上述案例看出,5台故障风机,其中4台为推力侧主轴磨损。例如2号炉l号引风机联轴器正确连接的磁力中小位置为150 mm左右,而实际的连接尺寸为155 mm。
2.4运行方式的影响
离心风机一般为人口挡板截流调节,风机应尽量避开不稳定运行工况区。风机运行时,因进出口存在压差,必然存在一定的轴向负荷。风机均有消除或减小轴向力的设计,如一期引风机即为双吸风机,但由于两侧进风不均尤其在挡板开度过小时,挡板开度处在入口气流涡流区域剧烈振动,曾多次导致挡板轴断裂。此运行工况对风机轴向载荷影响最大,如负荷调峰期不进行高低速倒运,单纯的用入口档板小流量截流调节导致风机轴向振动增加,会对轴承造成冲击而诱发转套,不利于风机的运行。单吸风机在并联运行工况不一致时,会因风量及风压的不一致导致单台风机运行工况恶化,轴向负荷加大。例如2004年5月13日9:00,1号炉1号一次风机推力侧轴承温度65℃,准备安装冷却风机冷却。9:20安装冷却风机过程中,发现风机入口挡板全关,就地检查测量轴承温度60℃(画面显示68℃)且逐渐上升,准备换油;10:00就地温度达到69℃(画面显示78℃)时换油,温度降至就地65℃(画面74℃);10:40左右温度继续上涨,正在进行第二次换油过程中,轴承温度已超过80℃,且温升加剧,风机停运。环境温度升高,致使风机轴承温度有所提高,属正常现象。但在处理过程中关闭该风机人口挡板,两台风机运行工况不一致,致使该风机轴向负荷急剧增加,运行不稳,轴承承受轴向负荷过大导致温升剧烈增加。以上两种运行方式是在运行期间诱发轴承转套的主要问题。
3、预防措施
根据以上的原因分析,在预防轴承转套的措施上,首先要在安装中杜绝各部件配合的装配尺寸偏差,保证配合公差满足标准要求,对于各相配零件的尺寸精度、形位公差及表面光洁度应满足装配标准,不符合标准的应进行加工修复。在装配工艺上,应杜绝不正确的轴承装配方法,保证轴承定位的轴向紧力。对于联轴器的校正安装,应确定安装的磁力中心位置,消除轴向力达到最佳的运行状态。
其次,应根据轴承运转中的油脂状态、振动的发展趋势对轴承的运行状况进行综合分析。
3.1润滑油监测法
对轴承使用的润滑油进行系统分析,了解轴承润滑与磨损状态,查明故障原因和部位,及时采取措施扼制事故发生。对于润滑油中的金属成分磨损颗粒的含量变化应做好跟踪记录。随着设备运行时间的延长,金属元素的种类和数量均会发生相应改变,根据变化趋势可以判断设备产生磨损的部位和状态。该方法适用于对故障进行早期预报,一般在风机投运后对润滑油定期进行抽检化验。主要根据润滑油中铁元素的含量来判断主轴是否磨损,由于此方法适用于磨损的早期判定,还要结合风机运行的振动参数来综合分析判断。
由表1可以清楚看到,当主轴存在磨损状况时,油中的金属铁、铬、铜的含量已达到换上新油后的2~3倍。
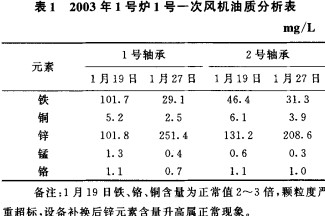
3.2振动判断法
旋转机械轴承故障在现场应用中复杂多变,主轴磨损后由于配合部位存在间隙会引起风机振动的变化,通常以振动信息为依据,对轴承转套故障进行故障诊断与监测可得到较好的预知效果。例如秦电一期的1号引风机推力轴承的跑套故障,在前期会出现如图5所示的故障特征,在轴承明显出现周期性的脉冲时,说明轴承已经发生了劣化。并且根据振动数据的趋势可以发现轴承的高频能量的增加,如图6所示,而由此进行轴承的检查,确认轴承内套的严重磨损,事后进行轴承更换及轴颈的处理,使轴承运行达到了稳定。如图7所示为修后的轴承的稳定状态的时域波形。
3.3停机检查法
如图8所示,适用于检修或故障检查时对磨损较严重的轴的检查。首先检查油箱内润滑油是否干净,主轴磨损后有大量铁屑沉积在轴承箱下面,润滑油呈黑色,主轴径向磨损的同时伴随着轴向磨损,轴肩或锁母部位产生间隙,因主轴磨损后程外大内小的倒锥型,轴承支撑转子的支撑点有所改变,外侧下面珠粒与轴承外套产生间隙,表现为松动,而外侧上面珠粒对轴承外套产生向下的压力,表现为卡涩。此检查法适用于对磨损严重且未进行解体测量主轴的快速判断。图8为主轴磨损时的轴承定位状态。
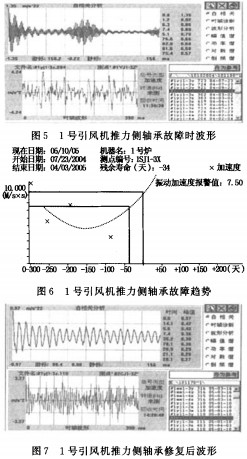
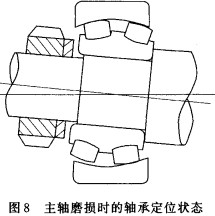
4、磨损后的处理方法
4.1刷镀法
是利用电镀技术将溶液中的金属离子镀在磨损主轴表面,使主轴尺寸达到配合要求的一种方法。其优点是镀层均匀,接触面积大,配合较好,修复时间短,适用于故障抢修;其缺点是刷镀前需对主轴进行仔细打磨去除所有毛刺及锈蚀,否则易造成镀层脱落。刷镀时对电流及温度要求高,控制不好同样造成镀层脱落。风险性较高,刷镀时要求连续性均匀盘车,否则将导致镀层不均,不适合盘车困难的风机抢修工作。因刷镀层一般不超过o.10 mm,故不适合磨损严重的主轴。双支撑风机主轴磨损的共性为:主轴磨损一般越靠轴肩部位磨损越严重,磨损后的主轴都带有一定锥度。而刷镀时电刷靠轴肩部位不一定刷到,刷镀完后主轴圆柱度偏差大。如2号炉1号引风机2004年11月检修,主轴磨损进行刷镀处理,室外温度低,连续刷镀14 h,运行时抢修,因无法进入机壳内部盘车,因此引风机主轴磨损抢修时不适合刷镀方法。3号炉A-次风机在2005年1月小修时因主轴磨损进行刷镀处理,刷镀后配合段轴向偏差大,仅有30%~40%的轴向尺寸达到配合要求,轴承装配后造成轴向摆动,导致风机启运时振动超标达0.10 mm,停运后对该轴重新进行研磨处理,恢复运行后正常。
4.2周向焊道法
是在磨损主轴圆周方向直接焊接焊道,然后将焊道进行锉销及磨销加工,使焊道部位局部达到配合尺寸的方法。其优点是修复时间短,适合故障抢修,不受磨损量的限制。其缺点是测量误差大,修复后轴颈配合接触为线接触,接触面积小,轴颈圆度偏差较大。预留紧力小时,装配后达不到配合紧力,预留紧力大时,易造成轴承径向的弹性变形,适用于对配合紧力要求较松的过渡配合。如1号炉1号引风机轴承配合要求为D200h7,1999年主轴深度磨损进行补焊修复,修复后运行良好,2000年更换转子时对轴颈进行检查,未见转套及磨损现象。3号炉B-次风机配合要求为D130m6,配合要求过盈量大,2004年7月因振动超标无法维持运行,停运抢修时同样进行焊道修复处理,在2005年1月小修时发现有磨损及转套现象,后来对该转子进行了补焊加工修复。
4.3补焊加工法
是将转子拆除,对主轴磨损部位进行补焊,然后将主轴放至车床、磨床上进行加工处理,直至达到装配的精度要求。其优点是加工精度高,各装配部件能够完全达到加工的精度要求,装配公差满足技术要求;其缺点是检修工作量大,检修时间长,不适合在机组运行时抢修,焊接过程因热量大容易造成主轴弯曲,修后需进行弯曲度检查及矫正,转子需进行动平衡试验,修复费用高且受场地限制。
以上3种方法各有利弊,须根根据工作的实际情况灵活运用。